

Cheney Wu
Class of 2025Detroit, Michigan
About
Hello! My name is Cheney and my Polygence project is on designing a new and effective airplane wing that would change its shape throughout flight according to outside factors (such as turbulence, load, and/or during different phases of flight). I chose to work on this project because I've liked airplanes ever since I was little and designing something related to it would be an awesome accomplishment, at the same time the process of designing would be good practice for what I want to do in university. After my project is complete, I would like to continue working on these small projects that come to mind by using the skills I've learned from this one.Projects
- "Exploring Autonomous Systems: Understanding how autonomous systems think, perceive, plan and act" with mentor Nate (Apr. 17, 2025)
- "An Airfoil Tensegrity Design: Concept, Algorithm Development, and Programming Implementation" with mentor Nate (July 19, 2024)
- "Exploration of Tensegrity Applications in Airfoil Designs" with mentor Nate (July 26, 2023)
Project Portfolio
Exploring Autonomous Systems: Understanding how autonomous systems think, perceive, plan and act
Started Mar. 9, 2025
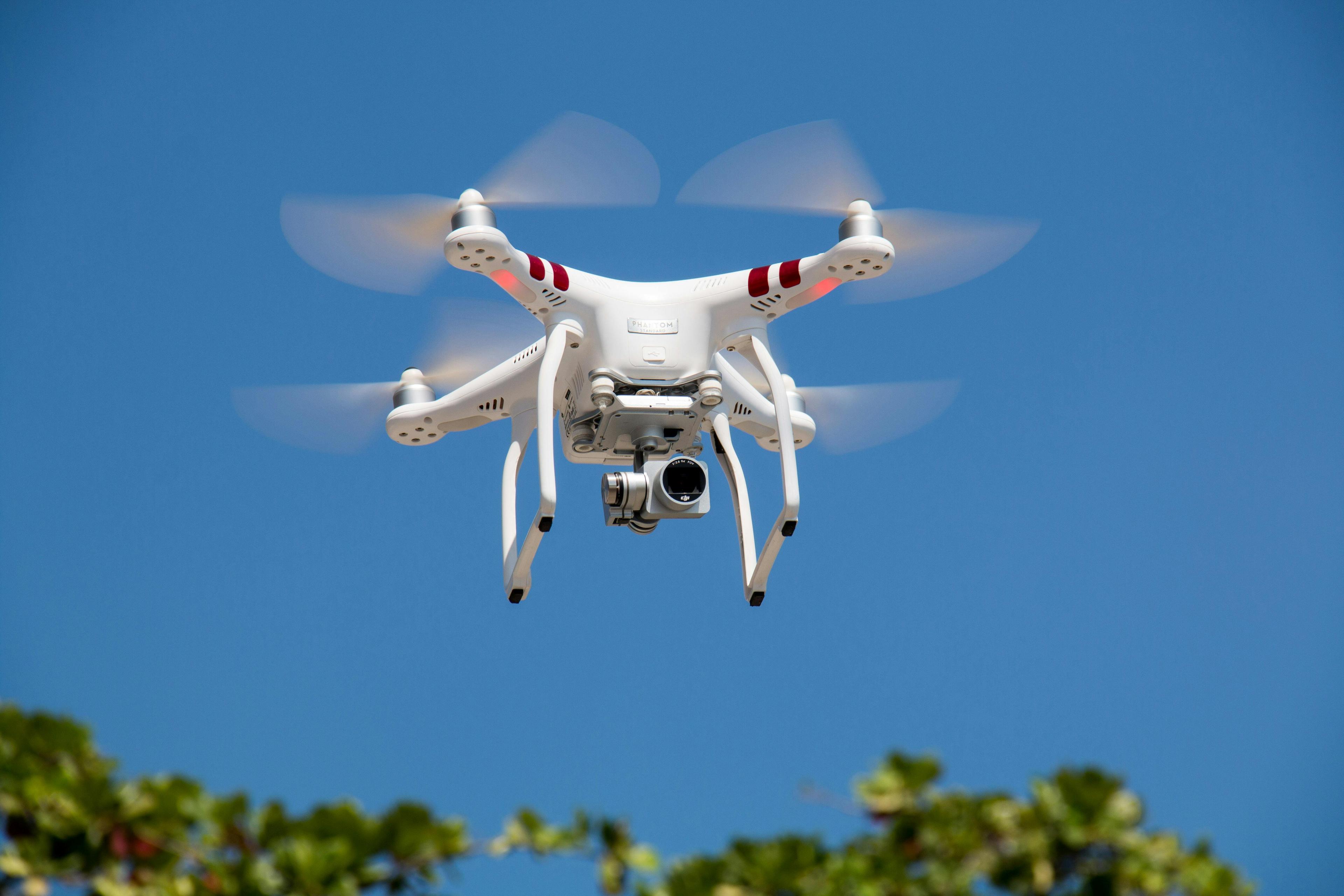
Abstract or project description
Self-driving vehicles, aerial drones, and humanoid robots have revolutionized day-to-day life in the 21st century. As these technologies mature, autonomous systems will disrupt supply chains, highways, and society. In this pod, we will investigate how autonomous systems sense, perceive, plan, and act. Students will learn the mathematical foundations of control theory, program their own computer simulation, and implement an industry-standard control algorithm known as PID Control. In addition, we will discuss emerging technologies such as Machine Learning Control and Computer Vision. After learning these concepts, students will write an original research paper on an autonomous system of their choosing. So, what are you waiting on? Grab a spot in this pod before a robot steals your seat!
Project Portfolio
An Airfoil Tensegrity Design: Concept, Algorithm Development, and Programming Implementation
Started Dec. 12, 2023
Abstract or project description
This paper investigates the potential of utilizing tensegrity structures to develop a new airfoil design methodology for achieving adaptive wing designs. By building on earlier research findings regarding an airfoil’s lift, drag, and pressure properties under the influence of various flight envelopes, this paper seeks to introduce a novel airfoil tensegrity design concept, incorporating a four-parameter variable system to streamline the computational design process, ensuring automatic node placement in each tensegrity structure. A dedicated program is developed for this process, and the effectiveness of this proposed algorithm is then demonstrated.
Project Portfolio
Exploration of Tensegrity Applications in Airfoil Designs
Started Sept. 21, 2022
Abstract or project description
In recent years, the aerospace industry has seen significant advancements in developing composite materials that offer a range of benefits. This paper proposes using tensegrity structures as a favorable supplement to further enhance aircraft design. Comprising a series of compression and tension members that are adaptive by nature, tensegrity structures can adjust the tension forces between the said elements to a desired configuration. Owing to the weight reduction they offer, tensegrity structures are an effective alternative over classic configurations of current systems on aerial vehicles. The paper examines several digital methods of plotting tensegrity structures in various NACA (National Advisory Committee of Aeronautics) recognized airfoils through Python programming. Following initial design concepts, more refined approaches are explored through digital modeling to better understand the advantages of using different tensegrity structures and how they can be combined to achieve maximum efficacy. Through discussing various digital plotting methods, an automated approach is discovered that provides the freedom to achieve any desired tensegrity design. By acquiring these models, many possibilities are opened for simulations in the future of the preliminary designs proposed in this paper.